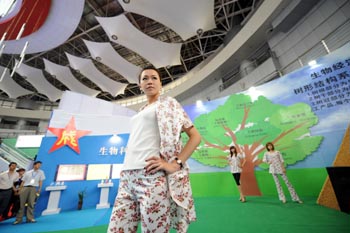 |
在第三屆中國生物產(chǎn)業(yè)大會上,由長春大成集團利用玉米為原料制作的服裝吸引了眾多參觀者的目光。資料圖片 |
位于全球黃金玉米帶上的吉林省,被譽為“鐵桿莊稼”的玉米卻一度成為吉林人的“包袱”--“儲不下、運不出、用不了”。1996年,以玉米深加工為主業(yè)的長春大成集團應(yīng)運而生,不但化解了多年來困擾吉林省的賣糧難問題,而且迅速崛起成為國內(nèi)最大的玉米深加工企業(yè),并躋身全球三大玉米深加工企業(yè)行列。
如今的長春大成集團,依靠自主創(chuàng)新實現(xiàn)了從深加工向精加工、從原料單一化向多元化、從技術(shù)引進向技術(shù)輸出、引領(lǐng)石油化工向植物化工四個“歷史性轉(zhuǎn)變”,化“危”為“機”開辟出嶄新發(fā)展局面,不僅帶動吉林省糧食深加工產(chǎn)業(yè)成為吉林省的三大支柱產(chǎn)業(yè)之一,而且為我國玉米深加工行業(yè)未來發(fā)展指明了方向。
從“深加工”向“精加工”轉(zhuǎn)變
在長春大成集團的會議室里,記者看到一棵碩果滿枝的“大成玉米樹”:樹的底部是玉米種植基地;樹干包括玉米淀粉、麩質(zhì)粉、纖維飼料和玉米油;樹冠是玉米精深加工產(chǎn)品,包括變性淀粉、淀粉糖、生物質(zhì)化工醇等八大類產(chǎn)品。
據(jù)了解,大成集團從1996年創(chuàng)立就提出,不能走單純的產(chǎn)能擴張之路,必須不斷由初加工向精深加工轉(zhuǎn)變,拉長產(chǎn)業(yè)鏈條,提高產(chǎn)品附加值,把玉米深加工發(fā)展成一個真正的黃金產(chǎn)業(yè)。到目前已發(fā)展為國內(nèi)最大的玉米深加工企業(yè)集團,年加工玉米300萬噸,產(chǎn)品主要有淀粉糖、氨基酸、生物基化工醇、變性淀粉、蛋白及纖維飼料等幾大系列一百多個產(chǎn)品,是世界最大的賴氨酸供應(yīng)商,在生物發(fā)酵、生物化工及非糧原料多元化上具有世界領(lǐng)先的技術(shù)優(yōu)勢,僅次于美國IDM和嘉吉公司,是綜合實力全球排名第三的玉米精深加工企業(yè)集團。
上世紀八九十年代,曾經(jīng)困擾東北廣大干部群眾的“東北現(xiàn)象”至今還讓很多人記憶猶新。特別是作為我國第一玉米大省的吉林,更出現(xiàn)了玉米“儲不下、運不出、用不了”的尷尬局面,成為名副其實的糧食大省、財政窮省。長春大成集團董事長徐周聞?wù)f,玉米深加工業(yè)轉(zhuǎn)變經(jīng)濟發(fā)展方式,必須限制初加工產(chǎn)品的生產(chǎn),通過政策引導(dǎo)和支持,引領(lǐng)行業(yè)向產(chǎn)業(yè)高端轉(zhuǎn)移。他說:“我們的淀粉生產(chǎn)已經(jīng)2年沒有擴大規(guī)模,2009年5月份前,行業(yè)不景氣加工一噸淀粉虧損500元,我們基本不再生產(chǎn)淀粉,而是從山東購買淀粉,自己主要生產(chǎn)下游產(chǎn)品,向精加工要效益。”
記者采訪發(fā)現(xiàn),大成集團擁有目前全世界最先進、產(chǎn)業(yè)鏈最長的玉米深加工企業(yè)群,十多個企業(yè)通過看不見的地下管道彼此相連,上游企業(yè)的產(chǎn)品通過地下管道源源不斷地輸送給下流企業(yè)作為生產(chǎn)原料,玉米完全被吃干榨凈,產(chǎn)品附加值從2倍、5倍到8倍、10倍,甚至幾十倍,同時省去了許多干燥、包裝、儲存、運輸?shù)拳h(huán)節(jié),使產(chǎn)品成本處于全行業(yè)最低的水平。大成集團總經(jīng)理辦公室主任王永安說:“在金融危機最嚴重的2008年四季度和2009年上半年,玉米深加工全行業(yè)虧損,我們?nèi)匀粚崿F(xiàn)了贏利,主要就是產(chǎn)業(yè)鏈條長,加工成本低,產(chǎn)品附加值高。”
業(yè)內(nèi)專家認為,大成集團立足自主研發(fā),走精深加工的路子,不斷提高產(chǎn)品附加值,向精深加工要效益,指明了玉米深加工行業(yè)未來發(fā)展趨勢,為全行業(yè)的發(fā)展做出了典范。
從原料“單一化”向“多元化”轉(zhuǎn)變
2008年,占全球玉米產(chǎn)量一半的美國實施了新能源法案,大量的玉米被用來生產(chǎn)燃料乙醇,引發(fā)了全世界對糧食安全的熱議,我國以玉米為原料的深加工企業(yè)也遭遇了原料瓶頸的制約。特別是飼料用糧的逐步增加,玉米逐漸由過剩變成供需平衡,遇有自然災(zāi)害等風險,甚至發(fā)生與人爭糧現(xiàn)象。
大成集團在國內(nèi)同行業(yè)中率先開辟原料“多元化”新路,糖蜜的利用在發(fā)酵產(chǎn)品獲得成功,秸稈制糖也取得重大突破,可有效替代玉米生產(chǎn)化工醇。專家認為,伴隨國內(nèi)玉米加工能力的不斷擴張,整體玉米供求形勢已經(jīng)開始發(fā)生微妙變化,近兩年來吉林省玉米加工企業(yè)經(jīng)常發(fā)生因原料緊張而導(dǎo)致減產(chǎn)、停產(chǎn)現(xiàn)象,大成集團在原料“多元化”方面的有益嘗試,使全行業(yè)對未來的發(fā)展看到了曙光,實現(xiàn)了有效的原料替代,產(chǎn)業(yè)未來的發(fā)展才有了出路。
普通秸稈制糖技術(shù),特別是利用秸稈制作乙醇等,糖的利用率低,資源消耗大,生產(chǎn)成本高,難以實現(xiàn)大工業(yè)生產(chǎn)。大成集團技術(shù)總監(jiān)褚臘林說,他們自主研發(fā)的用秸稈制糖生產(chǎn)化工醇技術(shù),含糖量占總量的57%,即兩噸玉米稈可制成一噸多糖,其成本相當于玉米糖的成本。
褚臘林給記者算了筆賬:玉米籽粒與玉米秸稈的成本比為1:1.6,全國每年玉米產(chǎn)量1.6億噸左右,秸稈產(chǎn)量約2.6億噸,如果把秸稈資源有效利用起來,全國農(nóng)民可增收1560億元,增收比例高達67%,又可帶動玉米秸稈的收集、運輸和加工制糖業(yè)的發(fā)展,有力支持農(nóng)村的工業(yè)化、城鎮(zhèn)化和農(nóng)業(yè)現(xiàn)代化。“目前小試已經(jīng)成功,正在進行中試,預(yù)計年底前能夠建廠。”他說:“我們率先實現(xiàn)了從玉米原料平臺向多糖原料平臺的轉(zhuǎn)變,為企業(yè)發(fā)展找到了更為廣闊的原料空間。”
從“技術(shù)引進”向“技術(shù)輸出”轉(zhuǎn)變
前些年,我國的玉米深加工企業(yè),多數(shù)是手工作坊式的生產(chǎn),一無人才、二無技術(shù),沒辦法只能花大價錢從國外引進,還經(jīng)常抬不起頭來。徐周聞帶頭創(chuàng)辦的黃龍食品工業(yè)有限公司,是我國第一個現(xiàn)代化的玉米深加工企業(yè),當初就采取了全套引進策略,從生產(chǎn)工藝到機器設(shè)備到軟件包全部從國外引進,付出了巨大的代價,但涉及一些關(guān)鍵技術(shù)時,外國公司卻明確表態(tài):多少錢都不賣。十年前,他們與全球較大的一家企業(yè)談技術(shù)合作,跑到上海去,等好幾天,人家最后只給五分鐘時間,而且堅決不同意將技術(shù)拿到中國來。
大成集團從創(chuàng)立伊始,每年投入科研經(jīng)費1億余元,先后建立了一個設(shè)計研究院、四個獨資或控股的研究所以及多個合作研究單位,常年聘請7位國外知名專家立足自主研發(fā),到目前很多技術(shù)已經(jīng)取得世界領(lǐng)先優(yōu)勢。褚臘林介紹說,6年前,外國人壟斷賴氨酸生產(chǎn)技術(shù),我國賴氨酸90%依賴進口,外國人以每噸6萬元的高價賣給我們的飼料企業(yè)。“大成人自主研發(fā),培養(yǎng)出具有國際先進水平、高效優(yōu)良的新菌種,開發(fā)出世界首創(chuàng)的65%賴氨酸新產(chǎn)品。”他說:“目前,全球賴氨酸總量100萬噸,大成就有60萬噸,占60%,有權(quán)制訂標準,左右全球市場價格。”
作為高效飼料必需的添加劑,大成的賴氨酸以先進的技術(shù)降低成本,過去五六萬元一噸的賴氨酸現(xiàn)在還不到1.5萬元,有力支持了國內(nèi)養(yǎng)殖業(yè)的發(fā)展。徐周聞回憶說,在2008年底一次會議上,全省養(yǎng)殖行業(yè)150多人集體給他鞠躬,他們認為由于大成賴氨酸的發(fā)展,有力推動了全國的養(yǎng)殖業(yè),全國飼料行業(yè)發(fā)展至少提速10年。
“科技創(chuàng)新、自主研發(fā)”不但支撐了大成集團的發(fā)展,也讓他們有了和外國大公司叫板的實力。兩年多來,有著近百年賴氨酸生產(chǎn)史的日本“味之素”公司,一直在美國及歐洲多國因知識產(chǎn)權(quán)問題起訴大成,形勢四面楚歌,大成一方面立足自主創(chuàng)新,另一方面積極應(yīng)對挑戰(zhàn),最終在美國“337”調(diào)查中把對方的專利打成了無效,是中國企業(yè)在“337調(diào)查”中全面勝訴的第一家。
褚臘林說:“我們培育出的賴氨酸新菌種,每一個基因都打上了大成的烙印,由于掌握了全球領(lǐng)先的技術(shù),也令外國同行刮目相看。”據(jù)他介紹,美國嘉吉公司總裁、可口可樂公司全球副總裁、韓國希杰公司總裁等多家世界500強公司高管都專程到大成集團考察洽談。如今,不少外國企業(yè)想用高價買他們的技術(shù),有的要求合資在外國建廠,大成集團不用投資一分錢,只需承擔建設(shè)和培訓任務(wù),就可并占有一定的技術(shù)股份。
專家認為,技術(shù)問題,是一個企業(yè)乃至一個行業(yè)賴以生存、發(fā)展、壯大的不竭動力,大成集團自主研發(fā)多項技術(shù)取得世界領(lǐng)先優(yōu)勢,是奠定其今天在世界玉米加工行業(yè)有一席之地的關(guān)鍵因素,企業(yè)要發(fā)展,行業(yè)要進步,就必須有技術(shù)做支撐,大成立足自主研發(fā)加強技術(shù)創(chuàng)新也值得國內(nèi)同行借鑒。
從“石油化工”向“植物化工”轉(zhuǎn)變
吉林省經(jīng)濟專家宋冬林認為,以石油為代表的化石資源,其資源的有限性已成為未來經(jīng)濟可持續(xù)發(fā)展重大隱患。大成集團利用生物質(zhì)資源開發(fā)替代石油的化工產(chǎn)品,生產(chǎn)出的植物化工醇受到世界很多大公司的廣泛歡迎,層次更高、戰(zhàn)略意義更大,“植物化工”的概念正在被越來越多的人所接受,率先引領(lǐng)全行業(yè)發(fā)展思路轉(zhuǎn)型具有重要意義,玉米地正在“長”出具有戰(zhàn)略意義的新興產(chǎn)業(yè)。
大成集團植物化工醇,從催化劑研發(fā)、生產(chǎn),到工業(yè)化的工藝技術(shù)、核心設(shè)備制造,均是自主創(chuàng)新,自主研發(fā)專利技術(shù)。產(chǎn)品有乙二醇、丙二醇、丁二醇等,不但可以替代石油產(chǎn)品,而且有石油產(chǎn)品不具備的優(yōu)點,是一種新型的化工材料。王永安說:“植物化工醇有許多石油基化工醇不可比擬的優(yōu)點,原料可再生,生產(chǎn)過程中低排放,清潔環(huán)保,符合當前世界發(fā)展潮流。”據(jù)他介紹,大成植物化工醇產(chǎn)品,以其綠色環(huán)保的特點,受到國外多家著名大公司的青睞,如今大成的產(chǎn)品不愁賣,各地經(jīng)銷商都搶著要貨。美國寶潔公司月用丙二醇2000噸,美國AOC公司月用1500噸,廣泛用于生產(chǎn)汽車風擋玻璃、內(nèi)飾材料、保險杠等;美國杜邦公司用作可降解纖維聚酯;美國可口可樂公司用于生產(chǎn)可樂瓶……
據(jù)了解,為了替代石油生產(chǎn)植物化工醇,大成集團從本世紀初就開始投入巨大人力、物力、財力,自主創(chuàng)新,探索以玉米、薯類、秸稈等可再生植物資源為原料,生產(chǎn)化工醇產(chǎn)品。2004年建成了2萬噸的中試廠;2007年建成了世界首座也是唯一一座年產(chǎn)20萬噸的大規(guī)模生產(chǎn)廠,2008年10月通過了科技部組織的全面驗收,并取得多項技術(shù)進步,單廠產(chǎn)能也由20萬噸提高到40萬噸,產(chǎn)品供不應(yīng)求。目前,他們正在全力建設(shè)興隆山百萬噸化工醇生產(chǎn)基地,預(yù)計2011年上半年投產(chǎn)。
宋冬林等專家認為,大成集團植物化工醇的出現(xiàn),以可再生資源有效替代了石油等資源,不僅實現(xiàn)了經(jīng)濟可持續(xù)發(fā)展,而且生產(chǎn)出綠色環(huán)保產(chǎn)品,符合新時期發(fā)展方向,將在世界范圍內(nèi)掀起一場由石油化工向植物化工的深刻變革。